Pre-Qualification of Mechanical Splices for Reinforcing Bars in Seismic Conditions
The use of reinforcing bar couplers or mechanical splices in reinforced concrete construction is on the increase. Mechanical splices are selected for various reasons: where lapped splices are impractical due to congestion of reinforcement, at construction joints and increasingly for practical considerations to enable build-ability, thereby simplifying construction.
This article provides a brief overview of the current testing related to mechanical splices and the background for such tests with a specific focus on the requirements for seismic applications.
Load Transfer
Generally, the transfer of load between reinforcing bars is achieved by lap splicing the bars. The load transfer mechanism for lap splicing is by cementitious bond and the effectiveness of lap connections is dependent upon the type of bar and the strength and quality of the concrete. Additionally, as the bars are laid side by side, the load transfer is indirect, whereas mechanical splices provide a direct in-line load transfer. Load testing the performance of lap splices is expensive and time dependent, as the reinforcement has to be cast in concrete. It is therefore seldom undertaken in practice.
In contrast, mechanical couplers are generally subject to extensive testing to meet the requirements of specific national standards, technical approvals or those of a state or national infrastructure owner.
Testing & Standards
The main technical requirements for mechanical splices are:
- Tensile strength and ductility under static loads; this is necessary to provide a factor of safety.
- Limitation of permanent set slip under static loads, often referred to as slip; this is necessary to limit cracking of concrete.
- Cyclic loading performance; necessary for structures in seismic (earthquake) regions.
- Fatigue performance; necessary for structures subjected to repeated loading, such as bridge decks.
The first two are considered essential for building construction applications; cyclic and fatigue performance are additional requirements for specific structures.
NZS 3101:2006, AC133:2010 and ISO15835:2009 all specify some requirements for mechanical splices. However, ISO15835:2009 goes further and covers all four categories of strength, slip, seismic and fatigue and is widely used as the basis for international requirements by major infrastructure owners or in countries where specific requirements do not exist .
The Standards that could be applicable in New Zealand are shown in table 1.
Table 1. Current documents with splice requirements
ISO15835:2009 | Steels for the reinforcement of concrete - Reinforcement couplers for mechanical splices of bars |
---|---|
NZS 3101:2006 | Concrete Structures Standard - Part 1 The Design of Concrete Structures |
AC 133:2010 | AC 133:2010 - Acceptance Criteria For Mechanical Connector Systems For Steel Reinforcing Bars |
NZTA Bridge Manual | Bridge Manual - Bridge Manual (SPM022) Third edition (2013) - Draft |
Tensile Strength and Ductility
A margin of safety against failure of a splice is required and it is also desirable that a degree of ductility is available at the splice location in a structure. Lack of ductility could result in little warning of possible sudden failure of the connection. Ductility is particularly important when designing couplers for use in structures subject to seismic loading, especially if their intended use is within the plastic hinge zones.
The properties of the reinforcing bar used in conjunction with a coupler have a direct effect on the overall performance of the splice. In New Zealand, the most commonly used ductility class is class E and its individual properties are defined within AS/NZS4671:2001(1).
Most international standards, including ISO 15835:2009 and AC133:2010 use the lower characteristic ultimate tensile strength (5% Fractile) values for their strength requirements. For ISO 15835 this results in a strength requirement of 575MPa for a 500 grade bar. However, NZS3101:2006 recognises that this means 95% of the bars supplied to projects would exceed this value and therefore not provide sufficient confidence that the bar will be the critical failure mechanism. NZS3101:2006 therefore uses the upper characteristic ultimate tensile strength (95% Fractile) values which result in a strength requirement of 690MPa for Class E bars. However, this could be as high as 840MPa as specified in the NZTA Bridge Manual and according to the specifications in AS/NZS4671:2001.
The ductility of the reinforcement is established by the value Agt, which is defined as the percentage total elongation at maximum force, Figure 1. This is the increase in gauge length of the test piece at maximum force (Rm), expressed as a percentage of the original gauge length. A minimum and maximum ratio Rm/Re between tensile strength and yield strength is specified in AS/NZS4671:2001 for class E.
ISO 15835:2009 adopts a minimum Agt value, measured in the reinforcing bar outside the splice, of no less than 0.7 x the specified characteristic Agt value of the reinforcing bar.
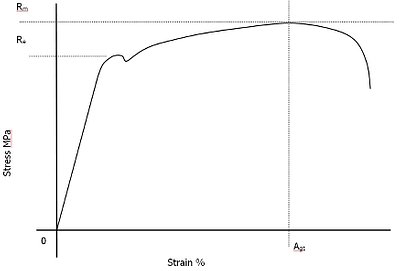
Figure 1 - Ductility Agt
The reduced Agt value for a splice connection is realistic due to the geometry, stiffness and mechanism of load transfer; a splice will behave differently from a control bar which simply strains under tensile load. A spliced connection is subject to movement comprising of two elements, strain plus slip, the latter element being due to the mechanical fit between the coupler and rebar. Due to this load transfer mechanism the Agt value of the spliced connection will in general be less than the straight control bar.
Permanent Set Slip
As concrete structures crack, the degree of the cracking under load is controlled by reinforcement provided by the designer. Design procedures for this are well-established in codes and regulations. For mechanical splices the most commonly agreed permanent set slip limit is 0.1mm. This is the limit in ISO 15835:2009 and is the accepted limit amongst many major infrastructure owners internationally. Current test procedures typically load a splice in tension from zero load, to a load equal to 60-70% (60% in ISO 15835:2009) of the reinforcing bar specified yield strength (Re), then return the load to zero, Figure 2. The permanent set slip is then recorded for the splice.
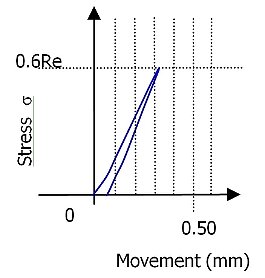
Figure 2 - Permanent Set Load Cycle
The measurement of permanent set slip is obtained by taking readings from two or three averaging Linear Variable Differential Transducers (LVDT’s) over a gauge length, Figure 3.
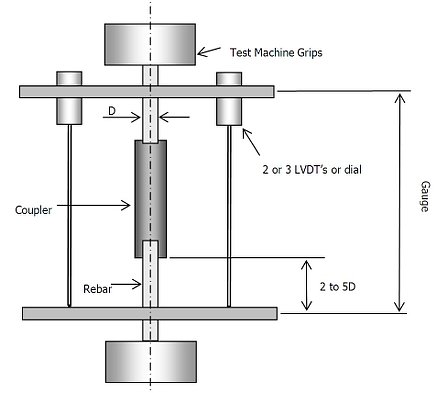
Figure 3 - Permanent Set Measurement
AC133:2010 has no mention of permanent set slip and the requirements in NZS3101:2006 differ from that of ISO 15835:2009. NZS3101:2006 asks that the specimen be loaded in tension from zero load, to a load equal to 70% of the reinforcing bar specified yield strength (Re). While under load, the total displacement across the coupler is recorded and must less than twice that of a single control bar measured over the same length.
Low Cycle Fatigue (Seismic) Performance
The performance of mechanical splices under cyclic loading is critical in seismic regions. However, the requirements for seismic behaviour differ greatly between New Zealand and other countries.
ISO 15835:2009 and AC133:2010 provide test requirements and guidance for elastic reverse loading; for moderate scale earthquake (S1 or Type 1) and large elastic-plastic reverse loading: for violent earthquakes (S2 or Type 2).
In ISO 15835:2009, S1 testing is kept within the elastic limit with an upper bound of 0.9fsy in tension and a lower bound of 0.5fsy in compression for 20 cycles. The limiting requirement is a permanent set slip of < 0.3mm. These products would be suitable where the risk of violent earthquakes was low.
In areas of higher risk, then the specification of S2 couplers would be necessary. The testing regime for this is 4 cycles with an upper bound of 2?sy in tension and a lower bound of 0.5fsy in compression with a residual slip of < 0.3mm. This is followed by a further 4 cycles where the upper bound is 5?sy in tension and a lower bound is 0.5fsy in compression with a residual slip of < 0.6mm.
A graphical representation of these tests can be seen in figure 4.
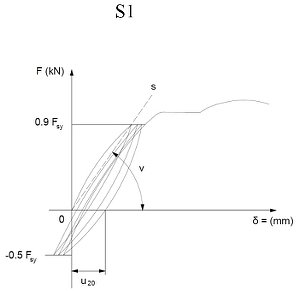
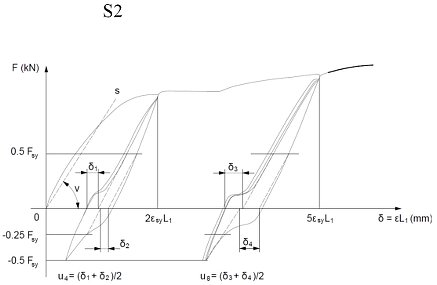
Figure 4
By combining the information gained from this reverse elastic/plastic behaviour with a sufficient strength and ductility, there is a good argument for such couplers to be accepted for use in plastic hinge zones.
In AC133:2010 the cyclic requirements are very similar to those shown in ISO 15835:2009; the only variation is that the upper bound for the elastic reverse loading is 0.95fsy rather than 0.9fsy.
NZS3101:2006 has a different seismic requirement, where the coupled connection is tested to an upper bound of 0.95fsy in tension and a lower bound of 0.95fsy in compression for 8 cycles with a residual slip of <110% of a control bar. This is a very stringent slip requirement and the limit is often lower than that permitted for the static slip tests. Also, as the standard does not provide a test method, it does provide a very real risk of the specimen buckling during testing. Alterations to specimen and gauge lengths are often carried out to reduce this risk, but will have an effect on the results gained.
High Cycle Fatigue (Dynamic) Performance
Where splices are used in structures subject to dynamic loading such as bridge decks, oil rigs or tall slender masts, the splice must display suitable fatigue endurance, in terms of stress and number of cycles. The results are normally presented in the form of a logarithmic S-N diagram (Wöhler curve), Fig.5.
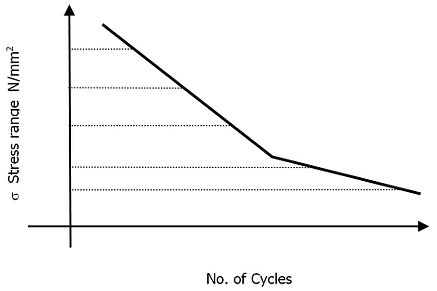
Figure 5 - S-N Diagram
Determination of fatigue performance requirements for a splice connection is probably the most difficult to standardise as test requirements differ internationally. Fatigue testing is also expensive because of the test machine time required to run several million cycles. As NZS3101:2006 provides no guidance in this area, ISO 15835:2009 provides a good base specification for fatigue testing.
Tests are either undertaken for four stress ranges and the stress ranges selected such that the slope of the two lines forming the S-N curve Fig.5 can be determined, this then gives an overall picture of the fatigue performance for a particular splice or by simply testing for 2 million load cycles with a single stress range; typically 60MPa.
Conclusion
In conclusion, test specifications for mechanical splices vary, dependent upon the specifying authority and country and application. Where mechanical splices are considered for use, the designer should ascertain the required coupler performance criteria and consult with manufacturers who can provide expertise in the selection of an appropriate and economical system.
References
AS/NZS 4671:2001 Steel reinforcing materials
Latest News
Ancon 500 Tension System renamed to Halfen Detan-D
As a future-oriented, innovative company, Leviat focuses on the ever-changing requirements of the industry, and our latest development combines the portfolio of Ancon and Halfen Tension Systems to ensure we meet the individual requirements of our customers.
ICC-ES Appraisal Report Issued to Leviat
We are excited to announce the ICC Evaluation Service (ICC-ES) has issued the first appraisal report in New Zealand to Leviat for Halfen HZA Anchor Channels and HZS Channel Bolts.